21. NOVEMBER 2024
A trio of experts for the mould making of the future
ZECHA, BCE and KRAMSKI: ceramic inlays in injection moulding tools
Extremely durable steels have traditionally been dominated modern mould making.
But how can a supposedly fragile material like ceramic revolutionise the industry? This is precisely the question addressed by this trio of experts – BCE Special Ceramics GmbH, KRAMSKI GmbH and
ZECHA Hartmetall Werkzeugfabrikation GmbH. Together, they are investigating innovative
approaches to injection moulding toolmaking.
Duos like Holmes and Watson or Batman and Robin complement each other with their different abilities and character traits, making them particularly successful and, therefore, popular. ‘The situation is similar for the two materials ceramic and steel in mould making, except that this dynamic duo is still more of an industry secret, unlike its popular role models,’ smiles Stephen Rapp, Product Manager at ZECHA Hartmetall Werkzeugfabrikation GmbH. ‘And we – BCE Special Ceramics GmbH, KRAMSKI GmbH and ZECHA – would like to change this in a joint project, because we see the potential for the injection moulding toolmaking industry and the entire sector to benefit from the greater use of ceramics!’
KRAMSKI GmbH – high-tech from the ‘Gold City’
KRAMSKI GmbH in Pforzheim is a global solutions provider of cutting edge stamping and injection moulding technology with approximately 700 employees worldwide. The company makes a significant contribution to the profitability of its customers by focusing on precision and bespoke consultation. With its constant development of products and tool technology, KRAMSKI is meeting the challenges of tomorrow with its state-of-the-art toolmaking today. The company’s areas of activity include the mobility industry, power electronics, medical technology, telecommunications, energy and environmental technology, as well as various industrial applications. Jörg Carle, Technical Director of KRAMSKI GmbH: ‘We produce around three billion parts a year to the highest precision, mostly plug contacts for the automotive industry, but also very small, delicate parts for hearing aids or blood sugar measuring devices and similar items in medical technology.’
Ceramic is not an unknown material at KRAMSKI, quite the opposite. ‘Among other things, we use ceramic coatings for injection moulding tools, where, for example, material build-up can be an issue.
That’s why we hope that the joint trials with BCE and ZECHA will enable us to use ceramic inserts going forward, thus eliminating the need for the coating process,’ Jörg Carle reveals. Of course, wear is also a major issue in mould making – not least when using glass-fibre reinforced plastics. ‘Even if we are working with steels in the range of >54 HRC, there is often a lot of wear, especially in the injection points area. This results in burrs forming on the component, which must be avoided at all costs, especially since they lead to excessive maintenance on the operating equipment. For the 16-cavity mould that we want to optimise in the current project, we are planning to make one cavity out of ceramic and use it for tests,’ explains Jörg Carle. And an experienced ceramics expert such as BCE Special Ceramics GmbH is the ideal partner for this.
The Marlin 3D series was specifically developed by ZECHA Hartmetall Werkzeugfabrikation GmbH for demanding applications in the machining of sintered ceramics and hard metals. Thanks to the latest laser technology, previously impossible tool geometries can now be applied to ultra-hard cutting materials such as PCD and CVD. The use of lasers means that these geometries can be designed to be even more delicate, precise and complex. Greater efficiency is achieved by extremely accurate geometrical tuning, which can be seen in excellent edge formation, precise dimensions and shapes, as well as in the outstanding surface quality of the component. Torus milling cutters, 6 mm in diameter and with 42 cutting edges, can be implemented within the MARLIN 3D laser series and are just one example of the almost endless possibilities offered by laser technology.
‘What I have seen of the MARLIN 3D milling cutters so far is impressive and has taken ceramic machining to a new level. Since the majority of ceramics are non-conductive and therefore cannot be
machined by die sinking, milling in the sintered state represents enormous progress and opens up new markets such as applications in mould making. We are having to completely rethink our approach, moving away from grinding with diamond-coated discs to milling technology with defined cutting edges, and we still have a lot to learn about the machining parameters in particular. But I have great hopes for the performance of ZECHA’s MARLIN 3D tools,’ says Torsten Prescher. Jörg Carle also sees the use of ZECHA tools as a major advantage: ‘If we can machine with μm precision to the highest surface quality on our milling machines, we will save a considerable amount of time and ultimately money in the production of the mould inserts!’
Tapping even greater potential in mould making
The three project partners are convinced: mould making offers significantly more potential than only
using steel. Through the targeted use of ceramic elements, tool life and process reliability can be raised to new levels, leading to a clear knowledge advantage and increased efficiency. ‘We are
excited about the development of this project and are sure that it will show us a new way of taking modern mould making to the next level of evolution,’ the partners explain in chorus. They hope to have successfully completed the project by early 2025 and will then be able to report in more detail on the progress made. ‘As soon as we have completed the project, we will of course share our results with the public – because we are more than a little proud of our idea and its implementation,’ says Stephen Rapp enthusiastically.
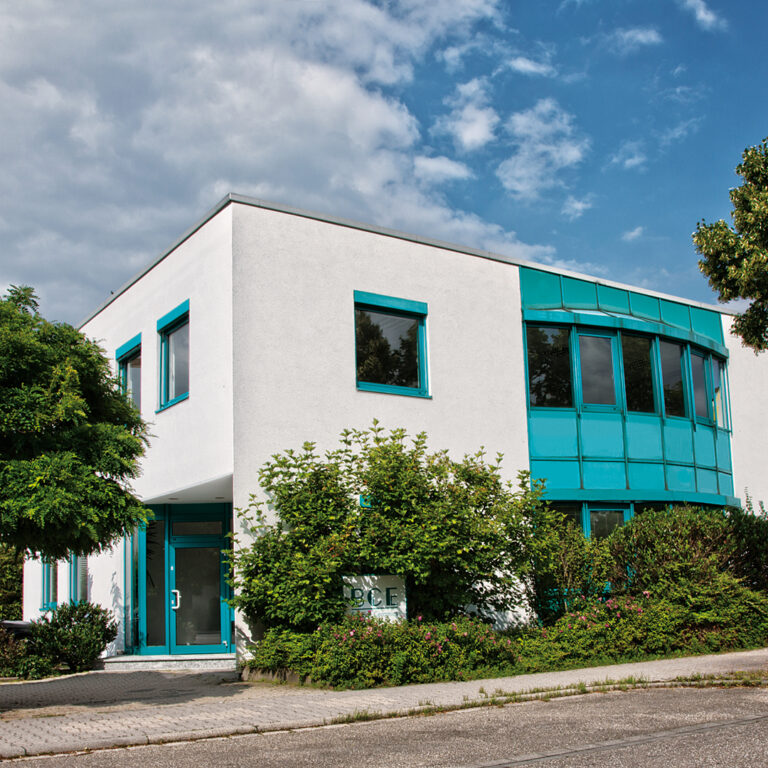
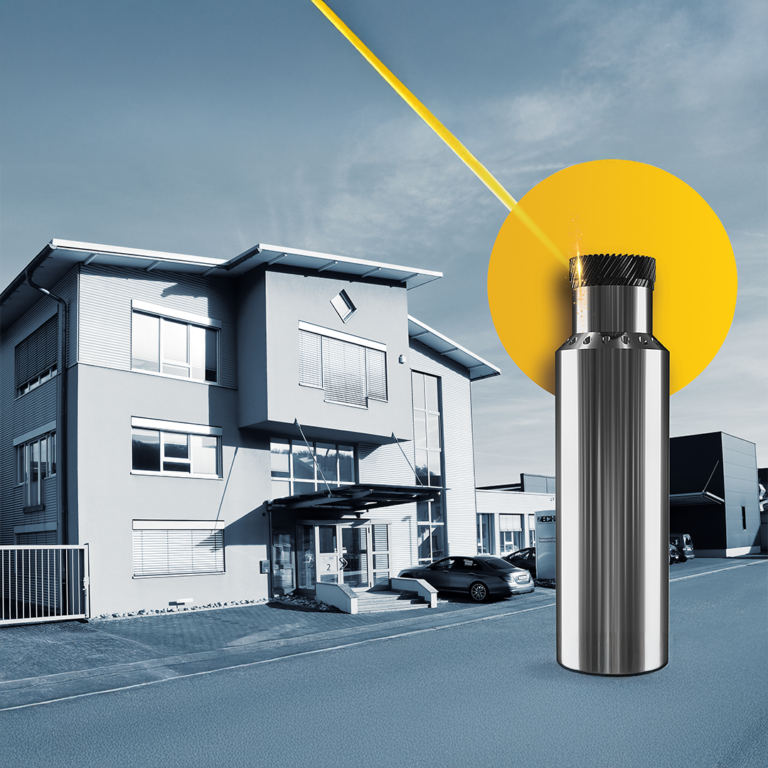
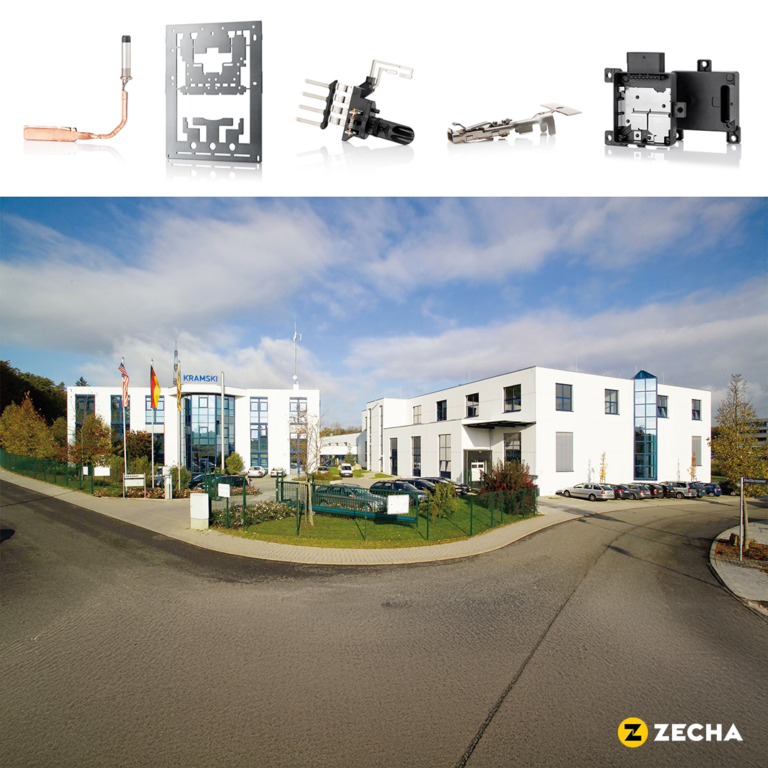
OTHER ZECHA NEWS:
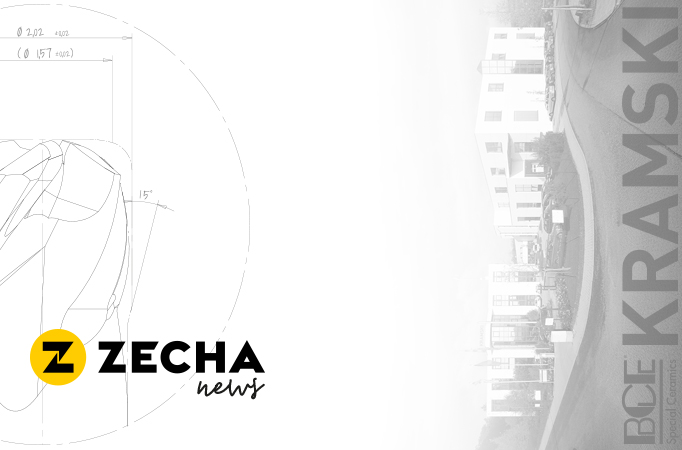
A trio of experts for the mould making of the future
But how can a supposedly fragile material like ceramic revolutionise the industry? This is precisely the question addressed by this trio of experts – BCE
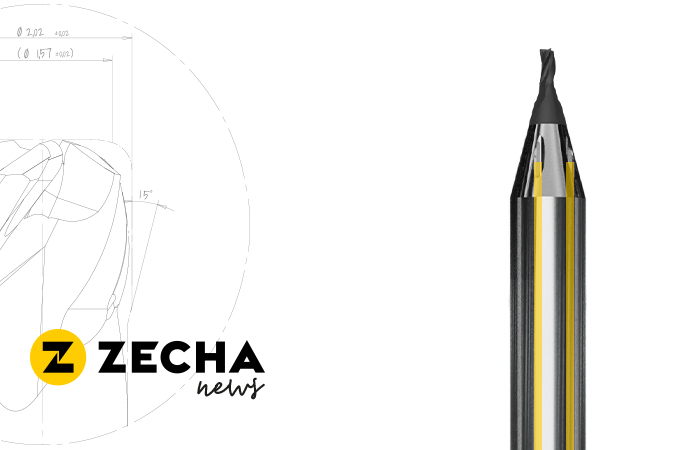
IGUANA with helix and shaft cooling system 931
ZECHA’s IGUANA line of mill cutters in diverse application-specific versions is known for its specific processing of the cutting edges by means of laser technology
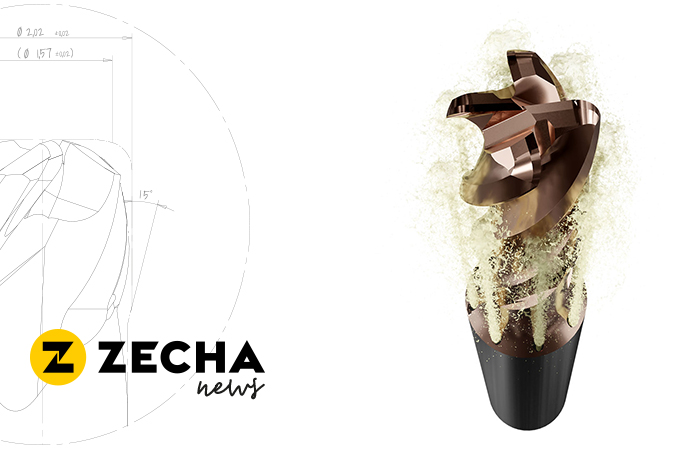
Steadfast with cool precision
Fast, accurate, and water-loving – these attributes aptly describe both the kingfisher bird and ZECHA’s new KINGFISHER line of tools. Based on the existing 455
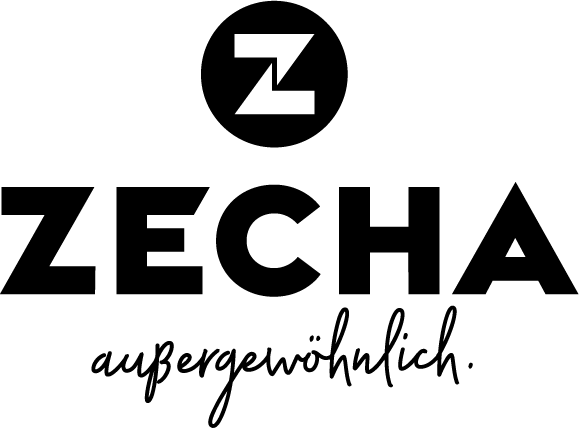
ZECHA Hartmetall-
Werkzeugfabrikation GmbH
Benzstraße 2
D-75203 Königsbach-Stein
+49 7232 3022-0
info@zecha.de
Cotact Page
Cutting Data Calculator