16. APRIL 2025
ceramic processing
Innovative methods in ceramic processing
Technical ceramics are very interesting as a material for components with an everincreasing performance. However, their hardness and low toughness make
processing extremely difficult. MPK Special Tools has good news on this front. The
precision technology specialists mill ceramics in the µm range and with
exceptionally sharp edges. They have everything for customer-specific component
production: innovative tools from ZECHA’s MARLIN 3D series, a wide range of
manufacturing processes and decades of expertise in the creation of complex
geometries with the tightest of tolerances.
The results at MPK Special Tools, the experts in high-performance tools and
components from Schwäbisch Gmünd, speak for themselves: a wide range of
manufacturing processes, such as milling, grinding or drilling, can be carried out on the
ceramic component made of partially stabilised zirconium oxide with the highest
precision and surface roughness in the nanometre range. Depending on the goal, this
can also be done with sharp workpiece edges and in a significantly shorter process time
than would be possible with elaborate grinding. ‘Micrometer tolerances in ceramic
milling can only be achieved by a very few manufacturing companies. This takes the
milling of technical ceramics to a higher level of performance compared to standard
processes. We can now also machine intricate, complex component geometries for our
customers, some of which could not even be produced by grinding, even more
efficiently by milling,’ concludes Christoph Steiner, MPK Plant Manager in Schwäbisch
Gmünd.
To date, the main techniques used to process high-performance ceramics have been
grinding and polishing. These proven methods can be used to produce high-quality
surface finishes with great precision without placing too much stress on the material.
The latter is crucial, because although these sintered ceramics are extremely hard and
can withstand high mechanical loads, they are also brittle and have low fracture
toughness. Machining techniques such as milling require a great deal of expertise and
have so far found it difficult to achieve such high levels of accuracy in the µm range.
Grinding processes enable greater precision but take a long time.
A ceramic processing revolution – thanks to innovative tools
The milling of ceramics is undergoing a fundamental revolution with a technology that
sets new standards for precision and efficiency, thanks to the MARLIN 3D-Laser series
tools from ZECHA Hartmetall-Werkzeugfabrikation GmbH. The micro-tool specialists,
based in Königsbach-Stein, use lasers to manufacture their innovative torus and ball
cutters, as well as spiral drills for ceramic and hard metal processing.
This technology can be used to precisely create extremely delicate, complex and
previously impossible geometries in ultra-hard PCD and CVD cutting materials. In
addition, it is possible to fit many more cutting edges than before, especially on small
tool sizes. One example is a 6 mm diameter toric milling cutter with 42 teeth. The high
number of cutting edges and the geometry matched to the material result in a better
distribution of the cutting forces and therefore less heat build-up. This is important
because excessively high machining temperatures can influence the properties of some
ceramic materials. Internal and shaft cooling also minimises friction and tool wear. On
the basis of the new laser technology ZECHA is able to manufacture special tools in any
conceivable form, such as slot milling cutters. Furthermore, the versatile ZECHA
programme also offers the possibility of efficiently machining ceramic green bodies with
diamond-coated tools.
All these advantages come into their own when machining ceramics, where the market
increasingly demands the highest surface quality, dimensional accuracy and process
reliability. Ceramic components are of interest for an increasing number of highperformance applications because technical ceramics can be made from a wide range
of materials with a wide variety of properties, some of which are unique, and can be
tailored to their specific application. The requirements in medical technology, for
example, are extremely high, since biocompatible ceramic implants, for example, need
to fit perfectly in order to minimise health risks. In the field of electronics, precision at
micro-level is required, as even minimal deviations in ceramic insulators, for example,
can lead to malfunctions. And in the aerospace industry, where ceramic components
are used in engines or heat protection systems, it is dimensional accuracy and surface
quality that determine safety and efficiency.
Impressive component manufacturing accuracy
MPK Special Tools guarantees this required extreme precision, surface quality, process
reliability and 100% reproducible quality in the best possible way: the CNC use of the
MARLIN 3D tools with the iQ300 from Makino offers repeatable 3-axis machining
precision down to the micrometer range, combined with advanced testing and
measuring technology. MPK’s trademark is the perfection of a wide range of
manufacturing processes over decades, including everything from milling technologies
to surface, internal and external grinding for ceramics. This makes it possible to adapt
the machining strategies to the specific and very different ceramic materials.
‘To make our extensive know-how available to our customers, we have produced a
component that reflects both the current requirements of the ceramics industry as well
as the manufacturing diversity and expertise in Schwäbisch Gmünd,’ explains Jannik
Kimmel, Head of CNC Milling. The component was given a high-precision internal bore
(Ø1±0.001mm). PCD torus milling cutter with 42 cutting edges, the eccentric machining
as well as the planar and bottom surfaces achieved a dimensional accuracy of 0.002
mm, surface roughness in the nanometre range (Ra < 50 nm), flatness within 0.001 mm
and radius tolerances of 0.005 mm. Torx geometries, fluting, chamfering and standard
threads could be machined with various tools with almost no chipping. Any chipping
that occurred was limited to a maximum of 5 µm in the grain size range. On the back of
the sample part, MPK’s expertise in ceramic grinding came into its own.
Our ceramic milling service: consultancy and rapid production from a single unit
order
‘Our many years of experience in the hard metal sector also helps us when it comes to
the high-performance machining of ceramics. We find customised solutions for
individual requirements, starting from a single unit order,’ says Jannik Kimmel.
Customers who order larger quantities benefit from the faster and more efficient
production that ceramic milling offers compared to grinding. This can make a significant
contribution when it comes to time to market. It also saves customers from having to
purchase the specialised, knowledge and cost-intensive tools, machines and
techniques for ceramic processing. ‘And as dedicated precision engineers, we can also
guarantee our ceramic clientele: With us, the µ is in charge,’ Christoph Steiner states.
(Infobox:)
MPK Special Tools GmbH
MPK Special Tools GmbH, based in Schwäbisch Gmünd, has been an expert in precision
engineering for over 60 years. Experienced and especially skilled in punching and
forming technology, as well as in the manufacture of special tools according to
customer requirements, the company offers solutions of the highest precision and in
any quantity for active parts made of hard metal and steel along the entire process
chain. MPK’s trademark is its extensive know-how in a wide range of manufacturing
processes, such as CNC grinding technology, start hole shooting, wire and die sinking
EDM, carbide milling, as well as finishing and shrink fitting, made possible by a carefully
selected range of state-of-the-art production machines. Their latest innovation is the
micrometer-precise CNC milling of ultra-hard ceramic materials. MPK Special Tools
GmbH a sister company of ZECHA Hartmetall-Werkzeugfabrikation GmbH in
Königsbach-Stein.
www.mpk-specialtools.de
OTHER ZECHA NEWS:
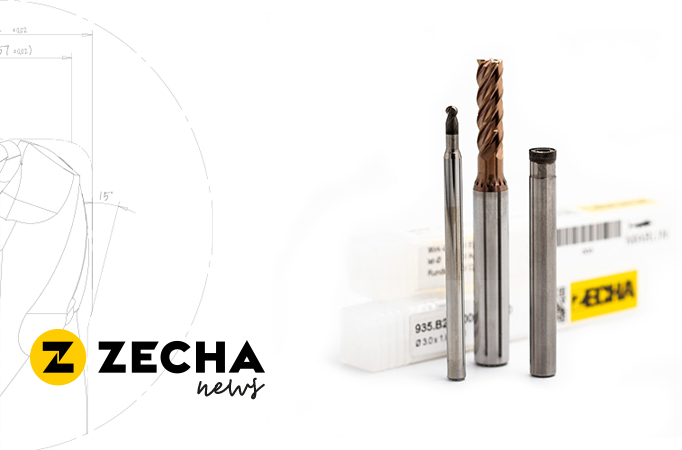
KLEINER GmbH and ZECHA
24-hour delivery: Made possible through regional proximity and a close, long-term partnershiph
With an impressive company history spanning more than three decades, KLEINER GmbH
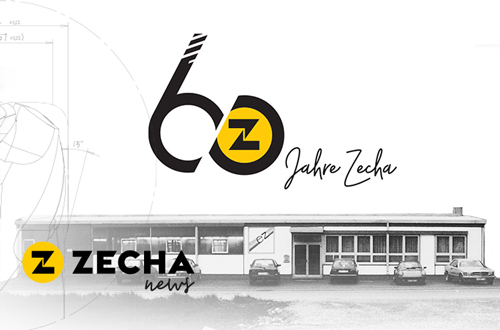
From 1964 to today – 60 years of precision
A special year lies ahead of us: six decades have passed since the doors of ZECHA first opened. Reaching this anniversary marks a significant milestone
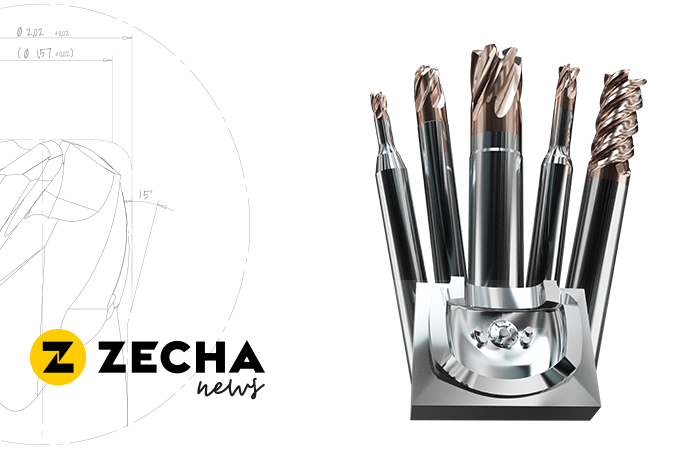
ZECHA and LANG
Precision in a double pack: The µm-precise production partnership
Precision in manufacturing doesn’t happen by chance: the µm only works when all components fit
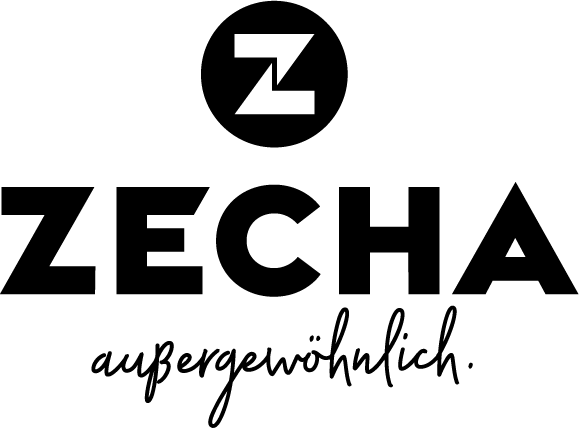
ZECHA Hartmetall-
Werkzeugfabrikation GmbH
Benzstraße 2
D-75203 Königsbach-Stein
+49 7232 3022-0
info@zecha.de
Cotact Page
Cutting Data Calculator